
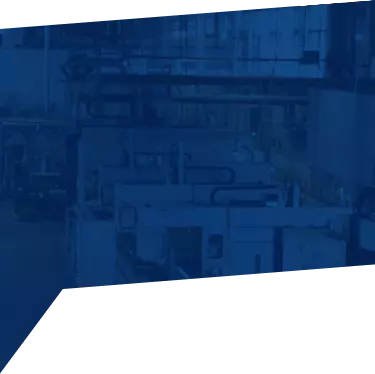
Years of successful operation of the enterprise
55 +
Production Units
4 500 +
Employees in the company's staff
1 800 +
Factory partners
100 +
ADVANCED TECHNOLOGIES AND EQUIPMENT
High-precision equipment, unique technologies and developments allow us to reduce production costs while maintaining high product quality
Unique production
The only specialized plant for the production of all parts of the cylinder-piston group in Russia and other CIS countries
URBAN-FORMING ENTERPRISE
The Company makes a significant contribution to the development of the economy of the Russian Federation and is a key taxpayer and employer in the Kostroma Region. The company employs more than 2000 people. The team is tightly integrated into the cultural and business environment of the region: employees participate in many "external" events under the "flag" of the company, off-site events of business organizations and authorities are held at the sites of the KZA itself. [Not Agreed]
ABOUT COMPANY
Russian world-class manufacturer
High-precision equipment and unique technologies allow KZA to bring products to the market that meet international quality standards.
The company is certified according to ISO: 9001 (Quality Management System Organization).
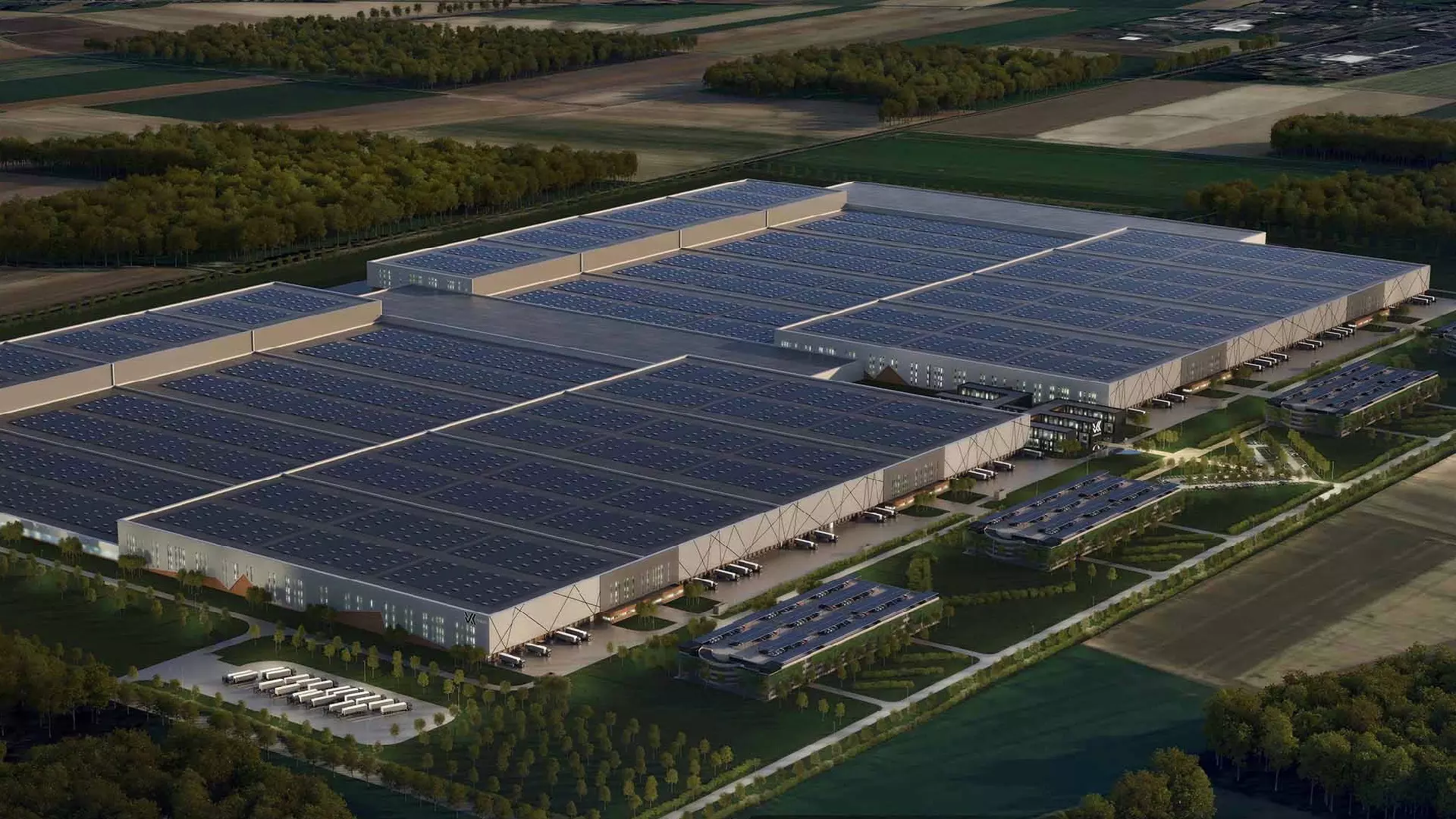
-
55 +
years of quality
-
40 countries
geography of supplies "Motordetal"
-
25 million
units of finished products per year
-
Official supplier
engine factories and automotive companies
News
All news